A Porsche produziu sua primeira caixa completa para um acionamento elétrico usando impressão 3D, conforme comunicado da empresa no final de 2020. A unidade de caixa de câmbio do motor produzida usando o processo de fusão a laser aditivo passou em todos os testes de qualidade e estresse sem problemas.
Os engenheiros do departamento de Desenvolvimento Avançado conseguiram realizar várias etapas de desenvolvimento ao mesmo tempo com o protótipo. A carcaça de liga fabricada aditivamente é mais leve do que uma peça fundida convencionalmente e reduz o peso total do inversor em, aproximadamente, 10%. Graças a estruturas especiais que só se tornaram possíveis devido à impressão 3D, a rigidez em áreas altamente tensionadas dobrou. Outra vantagem da manufatura aditiva é o fato de que várias funções e peças podem ser integradas. Isso reduz consideravelmente o trabalho de montagem e beneficia diretamente a qualidade das peças.
“Isso prova que a manufatura aditiva, com todas as suas vantagens, também é adequada para componentes maiores e altamente estressados em carros esportivos elétricos”, disse Falk Heilfort, gerente de projetos do departamento de Powertrain Advance Development no Porsche Development Center, em Weissach, na Alemanha. É concebível que o acionamento elétrico otimizado possa ser usado em um carro superesportivo de edição limitada, por exemplo.
A Porsche está impulsionando intensamente o uso de manufatura aditiva para otimização de peças altamente tensionadas. Há alguns meses, novos pistões impressos foram testados com sucesso no carro esportivo de alto desempenho 911 GT2 RS.
“Nosso objetivo era desenvolver um acionamento elétrico com potencial para manufatura aditiva, ao mesmo tempo que integrava o máximo de funções e peças na carcaça do acionamento, economizando peso e otimizando a estrutura”, afirma Falk Heilfort.
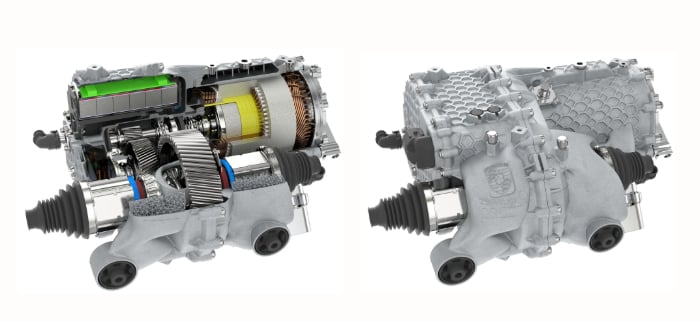
Nenhum outro processo de fabricação oferece tantas possibilidades e implementação rápida como a impressão 3D. Os dados do projeto podem ser enviados à impressora diretamente do computador, sem etapas intermediárias, como a fabricação de ferramentas. As peças são então criadas camada por camada de pó de liga de alumínio. Isso torna possível fabricar formas como caixas com dutos de resfriamento integrados em quase todas as geometrias. Cada camada é derretida e depois fundida com a camada anterior. Uma série de tecnologias diferentes estão disponíveis para esse propósito. A caixa da unidade foi fabricada com pó de metal de alta pureza usando o processo de fusão de metal a laser (LMF). Aqui, um feixe de laser aquece e derrete a superfície do pó correspondente ao contorno da peça.
Continua depois da publicidade |
A otimização do acionamento elétrico começou com a integração do projeto de componentes como mancais, trocadores de calor e alimentação de óleo. Isso foi seguido pela definição calculada por computador de cargas e interfaces. A determinação dos caminhos de carga ocorreu então nesta base. O próximo passo no método de desenvolvimento virtual foi a otimização dos caminhos de carga integrando as chamadas estruturas de rede. Essas estruturas inspiram-se na natureza e também podem ser vistas de forma semelhante em ossos ou plantas, por exemplo.
“Conseguimos expandir e melhorar nossas soluções de software e métodos para criar essas peças e agora podemos implementá-los virtualmente em um espaço de tempo muito curto”, disse Sebastian Wachter, especialista em Metodologia de Design e Otimização de Topologia no departamento da Powertrain Advance Development.
No entanto, a liberdade de design estendida oferecida pela impressão 3D também anda de mãos dadas com requisitos de design específicos. Isso inclui os engenheiros tendo que levar em conta o fato de que as peças de trabalho são produzidas camada por camada por fusão. Se houver grandes saliências na forma, elementos de suporte, como nervuras, podem ter que ser planejados. No entanto, eles não devem se estender para dutos de transporte de mídia. Portanto, é importante já levar em consideração a direção em que as camadas são construídas na fase de projeto.
Com a tecnologia da máquina atualmente disponível, a impressão do primeiro protótipo de caixa demorou vários dias e teve que ocorrer em dois processos de construção devido ao tamanho do componente. Com as últimas gerações de máquinas, é possível reduzir esse tempo em 90% e toda a caixa pode ser fabricada em um processo de construção.
O peso das partes da carcaça foi reduzido em, aproximadamente, 40% devido à integração de funções e otimização da topologia. Isso representa uma economia de peso de cerca de 10% em toda a unidade devido à construção leve. A rigidez foi aumentada significativamente ao mesmo tempo. Apesar de uma espessura de parede contínua de apenas 1,5 milímetros, a rigidez entre o motor elétrico e a caixa de engrenagens foi aumentada em 100% devido às estruturas de treliça.
A estrutura em colmeia reduz as oscilações das paredes finas da caixa e, portanto, melhora consideravelmente a acústica do acionamento como um todo. A integração das peças tornou a unidade de acionamento mais compacta, melhorou significativamente o pacote de acionamento e reduziu o trabalho de montagem em cerca de 40 etapas de trabalho. Isso equivale a uma redução no tempo de produção de cerca de 20 minutos. Um benefício adicional: a integração do trocador de calor da caixa de engrenagens com transmissão de calor otimizada melhora o resfriamento do acionamento como um todo. Este é um requisito básico para aumentos adicionais no desempenho.
Gostou? Então compartilhe: